In today's fast-paced industrial landscape, achieving optimal temperature control is crucial for ensuring the efficiency, reliability, and safety of various processes. This is where industrial thermostats come into play, serving as indispensable tools that regulate temperature with precision and consistency. From manufacturing plants to research laboratories, these devices have revolutionized the way industries operate, ultimately leading to enhanced productivity and cost savings.
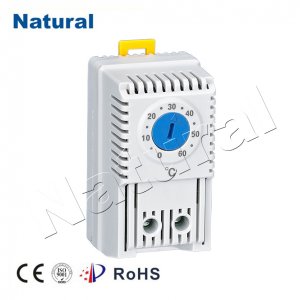
Industrial thermostats are advanced temperature control systems designed to maintain a desired temperature within a specific environment. They operate by sensing the temperature and then activating heating or cooling mechanisms to ensure that the environment remains within the desired range. The applications of these thermostats are vast and varied, spanning industries such as chemical manufacturing, food processing, pharmaceuticals, electronics production, and more. One of the primary advantages of industrial thermostats is their ability to provide highly accurate temperature control. Many industrial processes are sensitive to even slight temperature fluctuations, which can result in product defects or process inefficiencies. Industrial thermostats mitigate this risk by offering precise control, often with deviations of only fractions of a degree. This level of accuracy ensures consistent product quality and reproducibility in research and development settings.
Efficiency is another critical aspect addressed by industrial thermostats. Traditional temperature control methods often involve manual adjustments, which can be time-consuming and prone to human error. Industrial thermostats, on the other hand, operate autonomously once programmed, reducing the need for constant monitoring and intervention. This automation not only saves time but also improves overall process efficiency by maintaining optimal conditions without interruption.
Furthermore, industrial thermostats contribute to energy efficiency and cost savings. By maintaining a stable temperature range, these devices prevent excessive energy consumption due to temperature overshooting or undershooting. Many modern industrial thermostats are equipped with energy-saving features such as adaptive algorithms that optimize heating and cooling cycles based on real-time data. This not only reduces operational costs but also aligns with the growing emphasis on sustainability within the industrial sector.
The versatility of industrial thermostats is evident in their adaptability to various environments and requirements. They come in different sizes, configurations, and control capabilities to suit specific applications. For instance, in laboratory settings, precise temperature control is paramount for experiments and testing. Industrial thermostats can be integrated with other equipment, such as reaction vessels or incubators, to create a controlled environment conducive to scientific research.
In the food industry, maintaining specific temperatures during processing and storage is essential for ensuring product safety and quality. Industrial thermostats play a crucial role in regulating ovens, freezers, and cold storage facilities. They help prevent spoilage, extend shelf life, and adhere to food safety regulations.
In conclusion, industrial thermostats have revolutionized the way various industries approach temperature control. Their ability to provide accurate, efficient, and consistent regulation of temperature has led to improved product quality, process efficiency, and cost savings. As technology continues to advance, we can expect industrial thermostats to become even more sophisticated, further enhancing their role in shaping the future of industrial processes. Whether in manufacturing, research, or other sectors, the impact of industrial thermostats remains undeniable, setting new standards for precision and control.